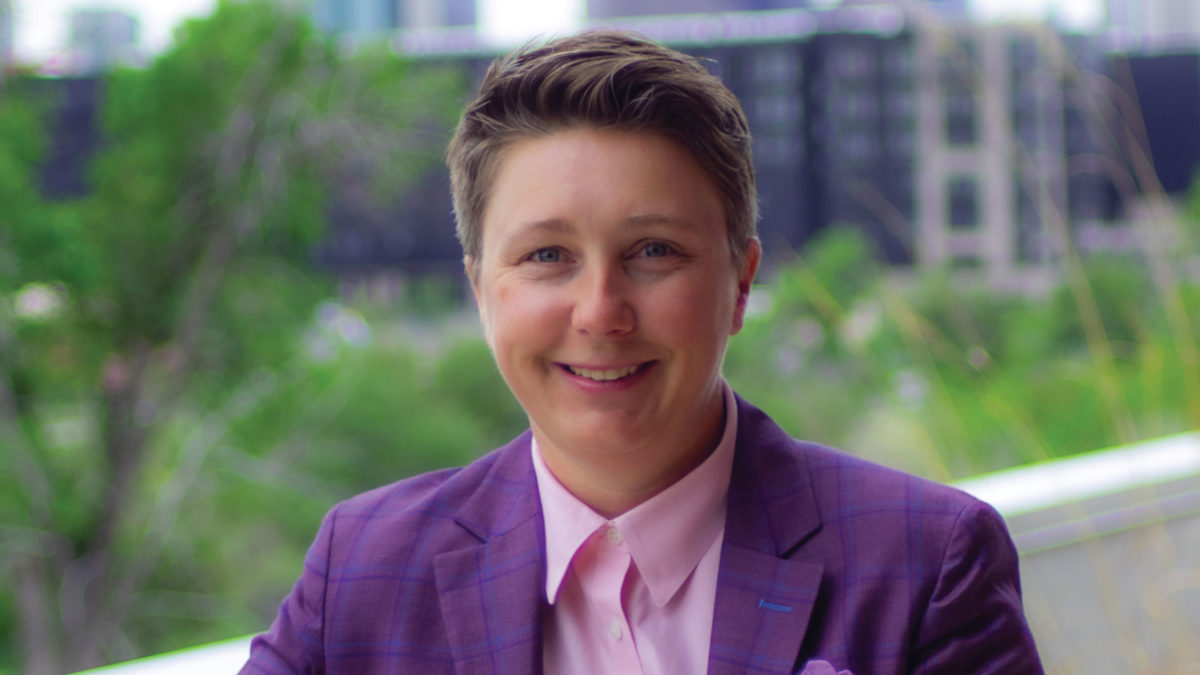
OSHA is Knocking
How to Prepare and Respond
July 2022
Download This Article (.pdf)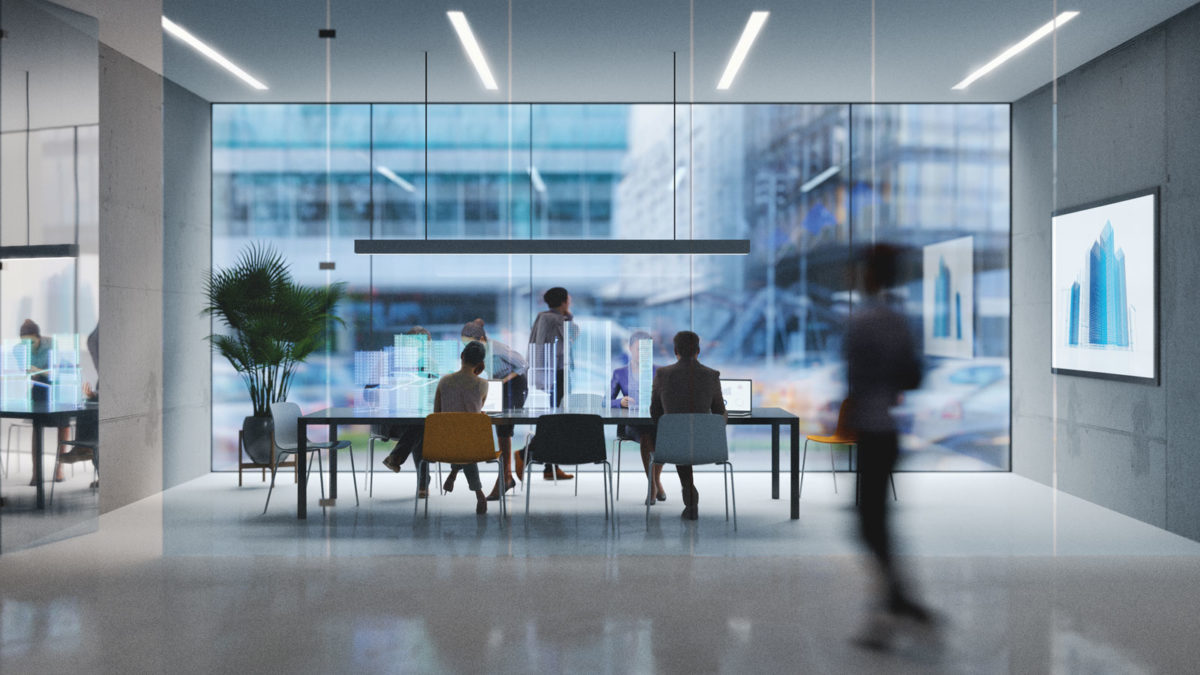
Occupational Safety and Health Administration inspections and enforcement action are on the rise. This article discusses how to prepare for and respond to these actions.
The Occupational Safety and Health Administration (OSHA or agency) has broad, widely applicable requirements that affect most employers. To successfully represent employer clients, attorneys must know which standards apply to the particular workplace, what potential outcomes to anticipate, and how to respond when OSHA inspectors arrive. This article offers tips on preparing for and responding to OSHA’s regulatory actions.
The Basic Requirements
In general, OSHA requires employers to provide a safe and healthful work environment for employees. This two-part mandate requires employer compliance with
- applicable OSHA standards; and
- OSHA’s General Duty Clause, by providing a workplace free from recognized hazards causing or likely to cause death or serious physical harm.1
Before the pandemic, many employers did not realize they were subject to OSHA’s requirements, but OSHA entered the spotlight when it became the lead federal agency in drafting COVID-19 regulations. Since then, OSHA’s budget has continued to increase, allowing for more inspections and enforcement actions as the country weaves in and out of COVID-19 restrictions.
OSHA’s Role
Congress created OSHA, which is part of the US Department of Labor (DOL), when it enacted the Occupational Safety and Health Act of 1970 (OSH Act). The OSH Act aims to ensure safe and healthful working conditions through its standards, and it applies to most private sector employers and some public sector employers in the 50 states and certain territories and jurisdictions under federal authority.2 The OSH Act can be administered in two ways: (1) a state can develop its own workplace safety requirements that are at least as effective as the OSH Act and obtain OSHA approval to implement the state plan (state plan states), or (2) federal OSHA can administer the OSH Act in states without state plans. Currently, OSHA has jurisdiction over private employers in 29 states, including Colorado.3
OSHA enforces the OSH Act and provides training, outreach, education, and assistance. Its inspection and enforcement authority has declined over the last 30 years, and during the height of the pandemic in 2020, OSHA inspections and enforcement actions reached an all-time low, decreasing by more than 50% from 1990.4 However, OSHA activity is now trending up, in part because employee safety was an early priority of the Biden Administration, as evidenced by its Executive Order on Protecting Worker Health and Safety5 issued on the administration’s first day. Since then, OSHA’s funding has increased by 12% in FY 2021 and another 4% in FY 2022. The agency is increasing its inspections and enforcement actions across industries while churning out significant new proposed rules and emphasis programs. With OSHA’s increased activity, employers must focus on compliance with workplace standards, preparing for inspections, and anticipating other OSHA actions.
Workplace Standards
All employers must promote workplace safety. This includes familiarizing employees with general standards, such as emergency action procedures, and ensuring compliance with more complicated processes, such as OSHA’s extensive Process Safety Management (PSM)6 requirements. Whatever the workplace situation, the first step toward complying with regulations and having successful inspections is for employers to understand their underlying obligations. This is often more complicated than anticipated. The repeat offender issues below are commonly the root causes of noncompliance with safety standards, but good management practices can stave off adverse consequences.
Turnover
Currently, employee turnover is a significant issue for employers nationwide, with the last two years (and counting) dubbed the Great Resignation. This can impact health and safety compliance if new employees are not properly trained. Consequently, as employees are hired, employers should provide new hire training that includes general safety training and industry-specific and equipment-specific training. Training should also be tailored to the specific position. For example, some positions may benefit from training on handling agency inspections, timely retrieval of documents, and agency communication protocols. Depending on the nature of the position, both classroom and on-the-job training may be needed.
Document Management
Many OSHA requirements have associated recordkeeping obligations, including maintaining records and timely producing documents. For example, OSHA’s Recording and Reporting Standard requires many employers to maintain and update injury and illness logs, and to produce such records within four business hours of an authorized government representative’s request.7 Employers should make sure employees understand recordkeeping requirements. Records should be promptly updated and maintained in a format and location that allows them to be timely provided upon request.
Similar (but not Duplicative) Regulatory Requirements
Regulatory agencies often have similar requirements for many safety-related obligations. For example, OSHA’s PSM standard aligns in many respects with the US Environmental Protection Agency’s Risk Management Program (RMP)8 provisions. If applicable, workplaces must comply with both regulatory regimes, but documents evidencing compliance with the RMP are not required to be turned over during a PSM inspection, nor would they necessarily indicate PSM compliance. Similarly, employers often conflate workers’ compensation requirements with OSHA-required recordkeeping and reporting obligations, which can result in compliance gaps. On the other hand, regulatory agencies often work together, and if OSHA identifies a possible violation of another regulatory regime, it may coordinate with other agencies to scrutinize additional areas. Therefore, it is critical that employers understand OSHA-specific requirements.
Inspections
Inspections can be conducted for a variety of reasons. They can be routine, conducted as part of an initiative, or responsive to an injury, illness, or whistleblower. During the pandemic, OSHA typically announced its inspections in advance, giving employers a heads up and time to prepare. However, with the recent easing of COVID restrictions nationwide, OSHA has returned to impromptu, unannounced inspections. In light of this, the best way to ensure smooth inspections is to stay on top of employee training.
Employers in highly regulated industries routinely have governmental inspectors in their facilities, so their employees are likely familiar with inspection processes. Other employers may lack significant experience with regulatory inspections, which underscores the importance of training and preparation. In any event, all employers should understand the following unique features of OSHA inspections.
Procedures
Employers have specific rights and responsibilities under OSHA. To safeguard these rights while remaining in compliance, employees must know how to effectively manage an OSHA inspection. This includes more obvious details such as asking inspectors for their credentials and about the scope of their inspection, having an employee accompany each inspector around the premises, using the most direct route to areas of interest, and protecting confidential commercial information. Multiple employees at the premises should have the necessary experience and training to facilitate efficient inspections, especially as workplaces continue to implement hybrid workplaces and grapple with worker shortages. Employers should walk their teams through the entire inspection process, from opening conference to closure (or issuance of a citation), so that the process runs as smoothly as possible.
Safety Violations
Assuming potential safety violations are identified during an inspection (spoiler alert: OSHA will find violations), employers should be prepared to move quickly. Items identified during the inspection should be abated during the inspection if possible. If abatement is completed by the conclusion of the inspection, the employer should inform OSHA during the closing conference. If items cannot be abated immediately, corrective action should be taken as quickly as possible, with OSHA kept informed about the progress.
Records Requests
Employers should request that OSHA document requests be made in writing. This minimizes the likelihood of miscommunication between employers and the agency, and provides a structure for employers to ensure that all requests are responded to in a timely manner. Counsel should be involved at this phase to assist with scoping requests, drafting responses, and understanding potential objections.
Post-Inspection Management
By statute, OSHA is required to issue citations within six months of a violation.9 If OSHA issues a citation, it will include the applicable regulations OSHA believes were violated, the abatement required to correct the violation, the deadline for abating the violation, and, in many cases, a penalty. Employers have 15 work days to determine whether to (1) allow the citation to become final, by paying the penalty and abating the violations in the timeframes provided in the citation; (2) ask questions or respond to OSHA via an informal conference; or (3) contest the notice.10 If the employer contests the citation, the matter will be transferred to the DOL’s Solicitor’s Office to prepare for a hearing in front of the Occupational Safety Commission.
Safety Experts
Employers should consider working with safety counsel, lawyers who specifically assist with safety matters and routinely work with OSHA. Safety counsel should be consulted immediately upon receipt of a citation to allow time to evaluate options and determine actions that make the most sense within OSHA’s incredibly short timelines. In particular, the time allowed for working with the OSHA area office offers a valuable opportunity for safety counsel to assess the citations and potential repercussions, including working through items such as citation reclassification and abatement timelines, before the DOL Solicitor’s Office gets involved. Employers should avoid the temptation pay a small penalty without considering the full impact of an OSHA citation.
Citation Consequences
The consequences of an OSHA citation may not be immediately obvious to employers. One primary concern is the citation’s effect on future contracts. For example, many bid documents inquire about the number and type of violations a company has incurred over a certain time period, such as whether the company had more than one serious, willful, or repeated citation within the last two years. The answer to this question can impact the likelihood of the bid’s success. Relatedly, citations are public records; anyone can easily access a summary of a company’s OSHA compliance history and obtain more detailed information through a Freedom of Information Act request. Other less obvious impacts include OSHA’s increasing penalties for repeated or willful violations and impacts on pending or future litigation.
Press
Although OSHA’s policy on whether and when it will issue a press release has varied over the last decade, employers should prepare for the possibility that OSHA will issue a press release when it issues a citation, prompting questions from customers, employees, boards of directors, shareholders, the media, and other sources. Employers may want to engage their internal communications team or an external communications firm to manage the response to a press release or other inquiries.
Anticipate OSHA’s Knock
Attorneys who routinely deal with regulatory inspections and administrative actions may assume that all agencies work the same. But OSHA is unique, and attorneys and clients should take specific steps to prepare for its knock, before OSHA arrives at the door.
Focus on Experience and Training
Experienced safety counsel and safety teams can make a big difference in addressing OSHA’s impromptu actions, rigid deadlines, and potential impacts. Safety personnel should be experienced in agency oversight and working with regulators and understand when and how to escalate issues to appropriate management staff. Further, all safety managers must be trained on how to participate in employee and management interviews with OSHA and how to respond to issues such as document requests, where safeguarding confidential commercial information is a priority. Even experienced safety teams can benefit from ongoing training on these items.
Understand National and Regional Initiatives
OSHA routinely creates priorities and engages in programs with national and regional emphasis. Region 8 includes Colorado, Montana, North Dakota, South Dakota, Utah, and Wyoming. Region 8 currently has local and/or regional emphasis programs in place for the facilities involved in aircraft support and maintenance, scrap and recycling, asbestos abatement, wood manufacturing and processing, workplaces with potentially high levels of noise exposure, automotive services, beverage manufacturing, grain handling facilities, roadway work zone activities, the oil and gas industry, workplace violence hazards at residential intellectual and developmental disability facilities, fall hazards within the construction industry, and silica in cut stone and slab handling.11 Employers with these operations should familiarize themselves with applicable OSHA program materials to understand how and whether OSHA plans to select sites for inspection, the applicable inspection procedures, and items inspections may focus on.
Track New Regulations
OSHA has a number of rulemakings in the pipeline that may significantly impact thousands of workplaces, so employers must stay on top of new developments. For example, OSHA is currently in the process of developing its first heat standard to protect employees from heat-related hazards.12 This is expected to be a broadly applicable standard that will require additional planning and preparedness related to heat exposure. OSHA also has announced dozens of other proposals expected to be promulgated over the next few years, including updates to the Hazard Communication Standard, infectious disease standard, and construction standards.13 Employers should choose their level of involvement in the rulemaking process according to their needs. Some workplaces can benefit from participating in public comment periods and submitting recommendations for improving a rule before it becomes effective. For other workplaces, remaining aware of new and prospective rules is sufficient and allows prompt compliance. In either event, having someone on the team who is up-to-date on the status of OSHA regulations enhances planning for future compliance obligations.
Plan Proactively
Employers can effectively plan for OSHA inspections by conducting internal inspections and audits of workplace safety standards. These can be performed by internal safety personnel, a safety consultant or lawyer, or, for some entities, in consultation with OSHA through its on-site consultation program. In any case, safety counsel should be consulted to determine if the inspection can be conducted in a way to provide it with attorney work product protections. Safety counsel can also help with other considerations, such as post-audit actions that would allow the employer to avail itself of safe harbor provisions in a subsequent inspection.
Conclusion
With OSHA’s increased funding and its renewed emphasis on worker safety, now is the time to get ready for its inspectors to come knocking. Attorneys and their employer clients can effectively prepare by following the suggestions above.
Related Topics
Notes
1. 29 USC § 654.
2. See OSHA Workers’ Rights, OSHA 3021-06R 2017, https://www.osha.gov/sites/default/files/publications/osha3021.pdf.
3. See OSHA State Plans, https://www.osha.gov/stateplans.
4. See OSHA’s 2020 Enforcement Summary (showing decreasing trends), https://www.osha.gov/enforcement/2020-enforcement-summary.
5. Executive Order on Protecting Worker Health and Safety (Jan. 21, 2021).
6. 29 CFR 1910.119.
7. 29 CFR 1904.40(a).
8. 40 CFR Part 68.
9. 29 USC § 658(c).
10. 29 CFR Part 1903.
11. See OSHA Directives—Regional LEP, https://www.osha.gov/enforcement/directives/lep.
12. 86 Fed. Reg. 68594 (Dec. 3, 2021).
13. See OSHA Unified Agenda (Fall 2021).
Experienced safety counsel and safety teams can make a big difference in addressing OSHA’s impromptu actions, rigid deadlines, and potential impacts.